By Meghan Wentland | Updated Jul 7, 2022 12:37 PM
We may earn revenue from the products available on this page and participate in affiliate programs. Uk Standard Fiberglass Smc Door
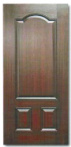
Nothing ages the appearance of a home in quite the same way as untidy seams and joints in spaces where the walls meet the ceiling, floor, and other walls. Smooth, finished walls require the techniques of a skilled plasterer or drywall finisher, but those top and bottom joints are difficult to perfect because as the home settles and shifts, any solid connection in those seams will be prone to cracking and splitting. To allow the surfaces to expand and contract while making sure the openings between the planes are sealed and finished, baseboard molding is often applied to the joint between the flooring and the wall, and crown or other decorative ceiling moldings are used at the joint between the walls and the ceiling. If your home doesn’t have these finishing touches—or if what’s there is old, banged up, or separated, it may be time to consider the cost to replace baseboards and other trims. Baseboards typically take the most abuse; furniture and vacuum cleaners whack into it, and little care is given to cleaning it, plus the floors can settle out from under baseboard molding, so it’s likely that yours could stand to be brushed up or replaced. Angi and HomeAdvisor report that the average cost to install baseboard is $1,170, with most people paying anywhere between $720 and $1,300. Looking to install new baseboard?A top-rated pro near you can help. Get free, no-commitment project estimates from baseboard installation pros near you. Find a Pro +
A quick walk down the molding aisle at a nearby home improvement store will show that there is an almost unlimited number of potential heights and designs for baseboard molding, so a homeowner will have to make a fair number of decisions while working up a reasonable budget for this project. There are several elements that contribute to the calculation of baseboard installation cost, including the cost of baseboards themselves, site preparation, and disposal, so it’s important to understand the options and how they’ll affect the total cost before beginning the baseboard installation project.
Not long ago, all baseboard molding was made of wood. The grade of the wood affected the price (and it still does), but all the wood would require finishing—stain and urethane or primer and paint—and then a careful installation using finish nails, caulk, and additional finish to achieve a smooth result. The market now includes a variety of materials that are lighter weight and easier to work with and install. Wood is still a classic option, especially if the homeowner is interested in an unfinished or stained look. Other options include PVC, polystyrene, MDF (medium-density fiberboard), and other products designed to make installation easier, and the costs will vary based on what you choose. Installation will also require nails, caulk, sandpaper, and potentially paint or stain.
Within the different materials, the various designs and styles allow homeowners to craft truly unique and custom looks for their home. Molding can range from simple square-edged boards tacked into the joint to elaborate stacked profiles that highlight the shape of the room or add glamour, and still others have designs carved or inscribed into the lengths of the molding. The more detailed and elaborate the style, the higher the average cost to install baseboard; pattern-matching in corners can require extra material, longer installation times, and more finesse with caulk.
Are you planning to add or replace all the baseboard in the home? Just one floor? Just one room? Or maybe a patch where a baseboard heater was removed? The larger the project, the more costly it will be, but “larger” doesn’t just refer to the linear footage of the molding. Jobs with many inside and outside corners require more material and more time spent cutting and trimming the molding to make the corner meet perfectly. Finding (or custom milling) molding to match the rest of the home in a single-room job can cost more than a simple replacement in a much larger area, as can finding a replacement piece for a patch. Simple, straightforward installations can be quite reasonable, but each added layer of difficulty will ramp up the cost.
How much does it cost to install baseboard? Molding installation does require experience and precision to install properly, so this is not an area where automatically hiring the least expensive professional is a good call. Walls, especially toward the floor, are not always flat and true, so an experienced installer will know how to attach and finish the molding to avoid gaps and cracks. Nail holes need to be filled, smoothed, sanded, and touched up, and painting molding once on the wall is also a job where experience makes a huge difference in the appearance of the final product. The labor cost to install baseboard trim will vary based on the local market and the complexity of the job. In general, the labor cost will run between $5.70 and $8.95 per linear foot of baseboard.
New baseboard can make your home even more beautifulA top-rated pro near you can help. Get free, no-commitment project estimates from baseboard installation pros near you. Find a Pro +
Usually, the installation labor cost will include the cost of cleaning up the project area and disposing of material generated during the installation, such as scrap wood, caulk, sawdust, and painting materials. But if existing molding is being removed as part of the project, the budget will need to account for the disposal of the old baseboards. If it’s a simple removal and disposal, expect to pay an additional $15 to $20 for this service. Some municipalities will allow this kind of construction debris to be thrown out with household trash—but only if someone removes all the nails and fasteners first. For large jobs, it may make sense to rent a small dumpster for haul away. And if the baseboard has layers of lead paint underneath a crust of latex, there may be special disposal costs associated with the appropriate handling and disposal of the lead paint to avoid polluting the local water runoff. These elements will add to the cost of the job as well.
Obviously the materials and labor will make up a significant portion of the total cost of replacing or installing baseboard in a home. However, they are not the only costs associated with this project, and some of the other components can actually be pretty significant, so it’s important that they be included in the budget if applicable.
If the home is a decade or more old, chances are there is existing baseboard molding in place that will need to be removed before fresh new molding can be installed. Old baseboard often has multiple layers of paint that may be caked into joints and adhered to the wall, and there are likely a number of nails that will need to be pried out before the baseboard can be broken up and disposed of. Removing this molding can cost between $50 and $100 per hour in labor costs, depending on the size of the room and the complexity of the removal. If this isn’t listed as a separate line item in the quote, ask about it so there are no surprises later in the job—it may be lumped into an expense titled “wall preparation” or “site preparation.” This is also typically an area where an enterprising homeowner can save a bit: As long as you have a pry bar and a utility knife, you may be able to remove the old baseboard yourself rather than paying a contractor to do it for you.
Baseboards are usually finished in a way that complements the style of the room. They may be finished with a clear sealant that enhances the natural wood and makes them easy to scrub, a stain followed by a sealant for a darker finish, or paint. Regardless of the option you choose, the finishing will likely be completed in two steps. It’s easiest to finish the baseboard before it’s installed, and then touch it up and smooth it after the installation is complete and nail holes are filled. This is another area where a homeowner can do some of the work on their own, but it’s important to make sure that you have the skill to do it well—a messy paint job or unprofessional finish will negate many of the aesthetic benefits of installing the baseboard in the first place. How much does it cost to install and paint baseboards? The cost will average $1,170 plus $1 to $5 per linear foot for painting.
When old baseboard is removed, it can leave a mark—many of them, actually. First, prying out the nails that hold the baseboard in place can tear or crumble the drywall behind it, and if the walls are plaster it can be even worse; whole pieces of the wall could fall out. Filling the holes and smoothing the surface in preparation isn’t difficult, but it does take time. More difficult to fix is the ledge of paint that can be left behind; after years of painting along the top edge of a baseboard, a crust of paint can be left adhered to the wall after the baseboard is removed. If the new baseboard is larger than the old, it’s a simple task of sanding down the old paint so the new molding can be attached, but if it’s a similar size or smaller, then more extensive repair may be necessary. Floors aren’t exempt from damage during removal, either, especially if the old molding has been caulked to the floor to seal out pests; sanding and refinishing may be necessary. These repairs average between $280 and $790. Should the walls require repainting after the repairs, the cost of interior painting may add between $970 and $2,760, depending on the number and size of rooms and the ceiling height.
There’s no rule book that says a baseboard has to be a particular shape, size, or color, so for those who are looking to jazz up their space with a subtle but effective customization, the baseboard can be a great opportunity. Layers of differently shaped molding stacked or overlapped can add architectural detail, as can custom corner caps or insets. Adding a line of colorful or wood-grain molding in a field of white can add style without overwhelming the rest of the space. The cost of these customizations will vary based on what’s requested, so it’s important to make sure that both the customer and the contractor are very clear on the desired outcome.
In addition to stylistic customizations, baseboard molding offers an opportunity to conceal wires and cables associated with delivering connectivity throughout the house. Channels through which wire can be run invisibly can be inset into the back of a baseboard, with caps set into the corners for access where appropriate. Again, this type of customization will vary in price based on the selected options and the distance the cables need to run through the molding, but the result can be a wire-free home—at least on the surface.
The various materials in which baseboard molding is available allow for homeowners in every budget tier to spruce up their homes. Each type of material provides different benefits and drawbacks. The weight and finish of each material creates opportunities to customize the look, and the styles range from simple to architecturally complex, so homeowners with a larger budget can meet or exceed the quality of their existing look, while those with a smaller budget can add grace and charm to their home without breaking the bank.
The least expensive material for baseboards, PVC, or polyvinyl chloride, is a type of plastic molding that won’t chip, crack, or bow, and it isn’t affected by water or dampness. It will not rot, and insects and pests will find no tasty morsels to gnaw on. Its low cost of $0.90 to $1.40 per linear foot makes it a great budget choice, and it’s ideal for areas that will be moist or wet, as it can be sealed with caulk to flooring and prevent water escape without causing damage. It’s not quite as forgiving as some of the other baseboard materials, so installers will need to be precise about placement and may have to work carefully on wall prep to ensure a smooth, tight fit. PVC is generally white upon arrival, so while it can be painted, it may not need to be.
Heavy and solid, MDF baseboards are stiff and can be difficult to use on uneven floors or walls. In addition, the composite nature of MDF means that coping the ends to miter corners can be difficult, and dents can occur during installation. Additionally, in spots where screws or nails are used, a kind of “reverse dimple” can occur, as the material pushes out around the nail head. This requires extra repair work to finish. However, the heaviness of the MDF can offer an elegant, solid look and feel at a much lower cost than high-end natural woods. Ringing up at $1 to $1.34 per linear foot, MDF offers a high-end finish at about half the cost of luxury woods.
Light, flexible, easy to cut, and easy to manage, polystyrene foam baseboard is made of a rigid plastic infused with air, so it’s solid but lightweight. It comes in a variety of shapes and profiles, and it can be purchased as an unfinished white or with a thin layer of wood veneer to use in applications where a natural wood-like finish is desired. It doesn’t expand or contract as wood does, although installation still has to account for the expansion and contraction of the walls and flooring. On the other hand, polystyrene molding usually only comes in shorter lengths, which means more seams to color-match and fill. Selecting polystyrene will result in a baseboard cost per foot of $1.15 to $1.65, so it’s a great budget option with a smooth finish, and it’s also excellent in applications where a lighter-weight material will make installation easier.
Don't know which type of baseboard is right for you?A top-rated pro near you can help. Get free, no-commitment project estimates from baseboard installation pros near you. Find a Pro +
Pine is the least expensive of the natural wood baseboard materials. At $1.40 to $1.85 per linear foot, pine boards need to be chosen carefully and checked for knots, bends, and bows and selected individually for the smoothest results. Ideal when installed unfinished in a log cabin or rustic application, pine can also be sealed and painted or stained, but the finish will rarely be as smooth as the harder wood options.
Poplar is a harder wood than pine and is less prone to cupping and bowing. It’s a clear wood, beautiful to paint or stain, smooth, and lightly grained. Poplar is a great compromise between the perfectly smooth fabricated moldings and the less-sturdy pine, and it costs between $1.90 to $2.50 per linear foot.
The midrange wood trims in maple and oak ring up at $2.50 to $5 per linear foot. These species come in several varieties each, but in general are hard and durable woods with defined grain. These are ideal woods for natural finishes that highlight the grain, such as stain or clear finishes, and will become deeper and richer with age. These woods can also be added as a layer along the bottom of a painted wood baseboard in the form of quarter-round or shoe molding stained to match hardwood flooring for a clean and beautiful transition from wall to floor.
These luxury woods are often clear-finished to let the beauty of the wood shine. These are hard woods, resistant to dings and scratches, and will stand up to years of hard use while retaining a look and finish that is extremely high-end and refined. The cost of $4.50 to $10 per linear foot seems like a lot, but the longevity of this material bears out the cost in reduced upkeep and replacement. A skilled installer should take part in the installation to endure a proper fit against the walls, and care should be taken not to split the hardwood during the application.
Base molding is the flat piece of material applied to the space where the wall meets the floor. It may be flat or have a shaped profile, and it’s usually less deep at the top than at the bottom. Traditionally the base molding will range between 3 and 5 inches tall. It can stand alone as a complete baseboard for a simpler look, or it can serve as the “base” upon which additional trim pieces or profiles are mounted for a more architectural look. Costs will vary based on the size and depth of the base.
Quarter round molding is literally one quarter of a dowel, split lengthwise, so there’s a 90-degree angle on the back side and a smooth, even quarter circle on the other. Tucked underneath or just over the edge of a baseboard, it can be used to blend the baseboard into the floor. Because it’s thinner and more flexible, it’s easier to bend it slightly to accommodate a floor that isn’t perfectly even and provide a seamless look. Sometimes this kind of trim is finished with the same paint or stain as the flooring, even if the rest of the baseboard is painted or stained darker. This look makes the seam between the floor and the molding nearly invisible. It can be used on its own for a very simple baseboard, but most often it’s used to visually connect larger molding with the floor.
Shoe molding is similar to quarter round molding and is used the same way. Rather than being a quarter of a dowel, however, shoe molding (so called because it is at shoe level) is slightly taller and narrower than quarter round. This gives it more height, but it takes up a bit less floor space as it doesn’t jut out from beneath the other molding as much.
Take a look at the joint between the flooring and the wall in your home. Is it perfect? Pristine? Precisely lined up? Chances are it isn’t. Flooring settles and walls can contract after installation, leaving unsightly gaps. If there’s already baseboard in place, take a close look: Are the seams between the molding and the wall crisp and sharp, or are they clotted with old paint with unsteady paint lines? Are they clean or rife with scuffs and dents? Baseboard molding is an element of a home that few people notice specifically, but do notice when it’s absent or scruffy, as it takes the appearance of the whole home down a notch without necessarily announcing itself. Why might new baseboard trim be a good idea?
As homes settle, baseboards that were perfectly mitered and butted up against each other can pop or crack. Ends can pop out, creating a vertical line in the middle of what should be a smooth expanse of trim, and corners can grow cracks and even fully separate. The usual fixes include caulk or wood putty, but over time, the continued expansions and contractions can render those fixes insufficient.
Also, part of the function of baseboard molding is to protect the wall from scuffs and scrapes. If the existing molding has done its job well for a while, it will have borne the brunt of those collisions, and while molding is harder than drywall, the damage will eventually begin to show. Shabby baseboard can take away from the rest of the space and make a home look poorly maintained, so if this is the case, it’s time to think about replacement.
Finally, many homes are heated with baseboard heating units, either as a primary or supplementary heat source. When heaters are installed, baseboard molding is usually installed up to the edge of the heater, with a space left for the heat itself. New baseboard heaters are frequently smaller and more efficient than older ones, which may leave an unsightly gap between the end of the molding and the edge of the heater. A contractor can try to match and blend a patch, but this is difficult, especially since the new pieces of molding will be pressed against the heater and will expand and contract differently than the rest of the molding. Installing new baseboard molding after replacing a baseboard heater will result in a smoother, neater appearance, so when budgeting the cost to install baseboard heat, it’s a good idea to include replacing the baseboard molding in the estimated cost.
Damaged baseboard?Replace it ASAP. Get free, no-commitment project estimates from baseboard installation pros near you. Find a Pro +
Another time to consider new baseboard is with the installation of new flooring. Usually flooring installation requires the removal of existing shoe molding so the flooring can run beneath the baseboard, or right up to it. While the larger baseboard molding may be salvageable, the shoe molding will likely be damaged during removal and will need to be replaced. If the older baseboard isn’t in perfect shape, it can be a great time to replace the whole baseboard profile.
Why does a home need baseboard molding? The aesthetic value of smooth transitions and clean lines aren’t debatable, but there are practical considerations as well.
Walls are soft; wood or manufactured molding is not. Thwacking a chair leg into a wall will cause a dent or potentially even a hole in a wall, requiring a multistep repair and repainting, while the same impact on a section of baseboard molding will likely leave no visible mark or, at worst, a small dent. Scuffs and scrapes are easily sanded down and repaired without much effort. Baseboard molding will protect the walls and provide a hard and durable field for impacts.
Insects and small rodents don’t need much space to get access to a home, and the seam between walls and floors presents a great opportunity for vermin to enter a home as floors and walls expand and contract. Baseboard molding bridges that gap and makes it easier to seal out unwanted visitors.
While cracks and gaps can serve as entry points for vermin, they’re also unattractive and can give the impression that the home has not been maintained well. Baseboard covers those imperfections and offers a smooth top coating. In addition, it will cover areas of the walls or floors that have begun to sink back or are unevenly taped, again covering problems that are unattractive but not structurally problematic.
The walls may be older, not as smooth or flat as would be ideal, and other surfaces in the home may not be as new or pristine as one might like. Baseboard and ceiling molding, along with door and window casements, provide a kind of outline of the home’s surfaces, directing attention to highlight architectural features. If the molding is clean, sharp, and fresh, especially if care has been taken to select a profile and size that works well with the style of the home, it can uplift the look of the whole space and draw the eye toward the lines the homeowner has chosen and gloss over the less-new finishes.
For homeowners who are confident about their ability to carefully remove existing molding, perform necessary repairs, and then reinstall and finish the baseboard, this could be a DIY job. Learning how to install baseboard isn’t necessarily difficult, but it requires a lot of practice and patience. The most challenging parts will be cutting the inside and outside corners to fit tightly together without bowing and with minimal need for caulk and putty. For those learning these techniques on the job, the practice can result in a lot of waste material or an excess of patch pieces and extra seams. This can mean the homeowner needs to repurchase materials lost to miscuts and extra expenditures for extra caulk. The same challenge will arise for less-experienced homeowners as they try to align the molding with uneven walls. It can be done, but it may not result in the expected cost savings, and homeowners may find they spend more time than anticipated, purchase new tools, and experience frustration when they end up with a finish that is less than professional.
Hiring a contractor means the result will be smooth and clean and properly completed, sealing out pests and allowing the walls and flooring to expand and contract. A qualified contractor will be able to create smooth joints and tight corners with the confidence of someone who has completed the task many times before, and will be able to make recommendations about profiles and styles that are suited to the materials and condition of the walls and flooring. In addition, contractors can often get reduced bulk pricing from home improvement stores. Finally, a professional will make much quicker work of the job than a homeowner who is figuring out pitfalls and workarounds as they go, and the results will be a finer finish than most DIYers will be able to produce. While the sense of accomplishment that comes from completing a new job yourself can be profound, baseboard molding is noticeable—very noticeable—and creates lines that you’ll see the imperfections in every time you look at them. It’s a good idea to have someone else to blame for any imperfections, and to have someone else you can ask to correct them.
Baseboard installation isn't a DIY jobGet free, no-commitment project estimates from baseboard installation pros near you. Find a Pro +
While the cost of installing baseboard molding is low in comparison to replacing the walls or flooring it connects, it’s still a pretty significant expense. There are several ways to save money and keep the budget in check without sacrificing the quality of the result.
As with any contractor you hire to work in your home, you’ll want to ask about licensing, insurance, schedules, and payment. Baseboard molding is a particularly visible job that requires precision and care, however, so there are some additional questions you should ask prior to hiring.
There are many different styles, materials, and options to choose from when beginning a baseboard molding installation project. You’ll have to make a lot of decisions, and choosing an experienced guide to help is a good idea. To get you started as you think about the options, these are some of the most common questions people ask about this project along with their answers.
The average cost to replace baseboards is $1,170, including materials and labor, plus an additional $50 to $100 per hour cost to remove baseboard that is already in place and dispose of it. Check the estimates you receive to make sure that they include the materials, labor, disposal, and finishing costs.
They can! If the baseboard molding in the home is damaged, old, or incorrectly installed, replacing it will favorably affect a buyer’s impression of the home as a whole, increasing what they’re willing to pay. Even if the trim is simply outdated, a fresh installation can create crisper edges that give the impression of a nicely updated home. The only occasion when replacing baseboards might not increase the value is in a historic home where the original molding is still in place and in excellent condition; in that case, the buyers will see the old but solid molding as an added value, not a liability.
Here’s a secret: Most walls are, on one plane or another, a little bit crooked. So the answer is that yes, a skilled professional can install baseboards on crooked, wavy, or tilted walls using a variety of tricks of the trade. Shims, glue, caulk, braces, and other methods allow a pro to compensate for the inconsistencies in most walls and produce baseboard molding that looks great.
If the flooring is already installed and perfectly level, and there are no plans to carpet the room, the baseboards can touch the floor. Otherwise, leaving a small, even gap between the bottom of the molding and the floor allows for carpeting to be added and can compensate for unevenness in the walls or flooring. If you’d like to leave the option open to add carpeting later, the baseboard can be installed leaving a gap, and then a thin rail of shoe molding can be installed to cover the gap. The shoe molding can be removed at a later time should carpeting be desired.
The labor cost to install baseboards per hour is approximately $50 to $100. You’ll be charged this amount for each hour spent removing the old baseboards and installing the new ones. This does not include material costs, which will depend on what you’ve selected, or the cost of wall and floor repairs (which can run between $280 and $790) or painting and finishing, which will add between $1 and $5 per linear foot. The quote you receive from a contractor should itemize these amounts; if you don’t see the labor listed separately, be sure to ask for clarification about what is and is not included in the quote.
You can, with some conditions. There are a number of occasions where it would be preferable to install molding without nails, including homes with heating pipes in the walls, lots of electrical circuits, or older plaster that may be damaged by forcing in nails. In those cases, molding can be installed using construction glue—as long as the molding is lightweight (ideally foam or lightweight wood) and quite flexible. Appropriate surface preparation is critical. Construction adhesive is very, very difficult to remove, especially if the surface is delicate, so you’ll want to get it right the first time. Make sure you clean and dry the surfaces beforehand, measure and dry fit all the pieces, and have a level handy, then work quickly and consistently to get the best fit and adhesion.
Copyright © 2022 Acton Media Inc. All rights reserved.

Fiberglass Interior Doors Articles may contain affiliate links which enable us to share in the revenue of any purchases made.